An OSRAM development team has created light that does not actually exist on Earth, and is using this UV-C light to disinfect surfaces, air and water. The recipe: Take an LED and add some highly specialized know-how and the courage to think outside the box.
What if you could disinfect the air in a room simply by switching the lights on for ten minutes? Or place a cell phone in a box for a few minutes to kill all the germs on it? It may sound futuristic but it’s already reality. This is disinfection with short-wave ultraviolet radiation – UV-C light.
UV-C radiation doesn’t actually exist naturally on Earth. It is absorbed by the ozone layer before it can reach us. Which is a good thing because short-wave light has such high energy that it can break the chemical bonds in an RNA or DNA helix. Genetic information is destroyed as a result. This has the positive effect that viruses or bacteria cannot multiply and will no longer be infectious. So UV-C light is a highly promising tool for successful disinfection.
But this radiation not only destroys the cells of viruses and bacteria, it can cause serious damage to our skin or eyes. Contact with UV-C light is dangerous, so protective clothing is essential.
Systems that use light to purify the air are currently equipped with conventional gas discharge lamps as the light source. They do, however, have a crucial disadvantage in that mercury can leak out if they break, making them unsuitable for mobile applications except in certain specific circumstances. Unlike the light emitting diode, or LED for short. The LED is small, versatile, durable and vibration-resistant – and it can emit UV-C light. A germ killer you can take anywhere is therefore tantalizingly within reach. The challenge right now can be summed up in one word: efficiency. At just four percent, the UV-C LED still has plenty of room for improvement here. And that is precisely the focus of the OSRAM team.
Developers at OSRAM are working on a breakthrough. A task that requires creativity, perseverance and an acceptance that there will be setbacks. And a particularly exciting task for the team.
Who is behind the technology?
High-tech needs people. And these people need high-tech. See for yourself who the creative minds are behind the technology of the UV-C-LED.
Predevelopment: the search for the perfect semiconductor
Hans-Jürgen Lugauer:
makes semiconductors emit light
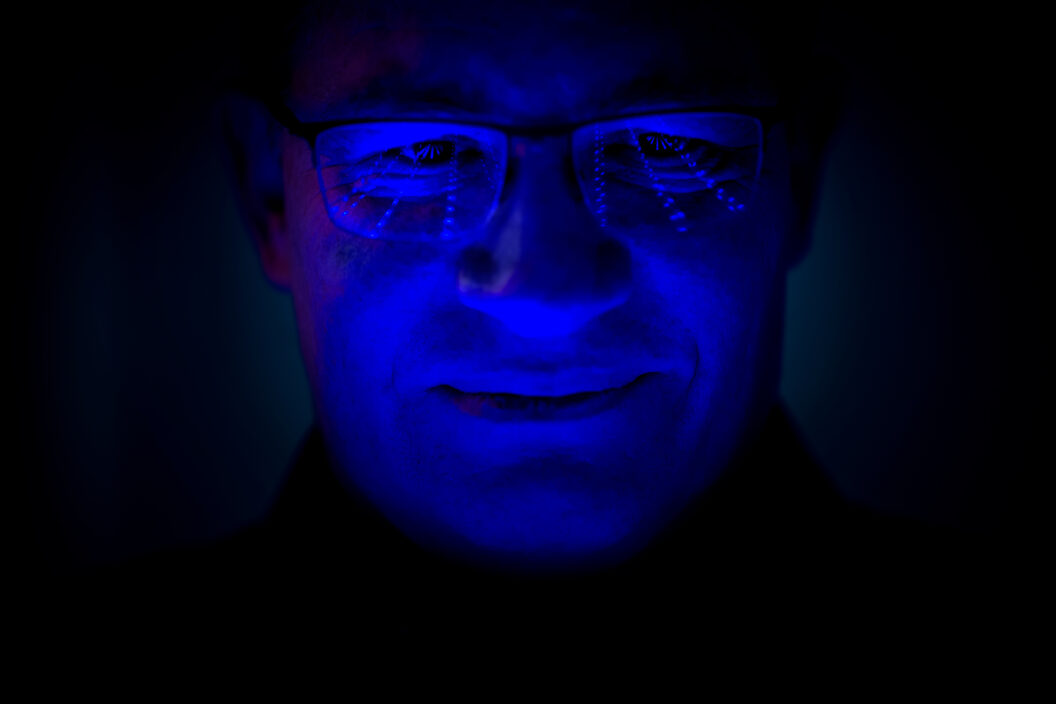
Hans-Jürgen Lugauer is used to setbacks. “If you can’t deal with setbacks then predevelopment is not the place for you”, he says. Lugauer knows what he is talking about. After all, he has been working at Osram since 1999. It was his first and only job application after completing his doctorate at the University of Würzburg, and for Lugauer to this day it’s a perfect match.
“I love this job. It’s great fun and suits me just fine. Obviously, there are times when things don’t go so well and after investing lots of time and effort I have to start all over again. I have to be able to deal with that.” But he couldn’t imagine it any other way: „I don’t want to do anything if I don’t know why I’m doing it. A routine job would not be for me – I need a certain challenge.” After working on the development of LEDs for the visible spectrum, his challenge now is to develop LEDs that emit UV-C light.
The fun of cracking a hard nut
Lugauer’s tasks have changed over time. He is now to be found more at his desk than at a laboratory bench. Does he miss the hands-on approach? “Yes, I really miss that. I keep getting the itch to do something actively myself. But I try to stay as close to the technology as possible so that I can still understand problems in great detail. A management job pure and simple without a technical connection would not be for me,” he added.
“I try to stay as close to the technology as possible so that I can understand problems in detail.”
Whenever it gets really tricky, he likes to take a little time-out alone to get to grips with what it’s all about – and then discuss his thinking with the team. Without this interaction with his colleagues he would not be able to move forward. It’s one of the most important elements of his work.
He likes the creative collaboration that is possible and indeed essential in predevelopment. “I’m creative, and that goes hand in hand with being a little unstructured. I’m working hard to keep this within limits,” he admits with a laugh.
Lugauer laughs a lot – even at work: “It’s important to me that we retain a sense of humor. We laugh a lot, even at normal everyday things. It’s something that motivates me and my colleagues. If I didn’t have fun, I wouldn’t be happy.”
Light with social relevance
Together with this motivated team, he now creates light that renders viruses harmless. That gives his work another special meaning, as he explains: “It feels good that small, mobile devices with UV-C light will soon be able to disinfect the air in a room, for example in hospital wards, so that fewer people die from bacterial and viral infections. We are developing something really relevant for society here. With our UV-C-LED we can replace the mercury lamps that have been used so far. That would be a huge leap forward for the health of the population and for the environment. That gives me a really good feeling.”
The Basis:
the semiconductor crystal

Aluminium gallium nitride (AlGaN) is the basis for UV-C light. This semiconductor crystal is a compound of aluminum, gallium and nitrogen. This means that UV-C-LEDs are fundamentally different from blue LEDs, on which the commercially available white LEDs are based. The compound for blue LEDs is indium gallium nitride (InGaN). To achieve UV-C light the developers replaced the indium with aluminum. Sounds simple but it’s not, because the two compounds have different material properties. Which means that AlGaN behaves completely differently from InGaN. As a result, new development and manufacturing processes are also needed.
Shine on you crazy crystal
The big challenge is to make the material emit light. That’s not something it does by itself. The AlGaN semiconductor is a very good insulator even at room temperature. This essentially non-conducting material only becomes a conducting material through the selective addition of atoms. This process is called epitaxy. In the chemical deposition process, the raw materials are transferred to a reactor in gaseous form where they react with each other under extremely high temperatures of well over 1,100 degrees Celsius on a suitable layer known as a substrate.
The conventional silicon used in the semiconductor world is unsuitable as a substrate because the grid spacings of the two crystals differ too much and UV-C radiation is absorbed. In most cases, aluminum oxide (Al2O3), also known as sapphire, is therefore used for blue, green and white LEDs based on InGaN. Sapphire is also the substrate of choice for producing UV-C light in the case of aluminum gallium nitride because its physical properties match very well with those of the semiconductor. It is also transparent for UV-C radiation.
Wafer thin
The epitaxial process itself is largely the same as in the production of conventional LEDs. Well over one hundred wafer-thin layers are deposited one on top of the other. The most important ones, the so-called “quantum wells”, are thinner than ten atomic layers. However, a lot of theoretical work is needed to ensure that the LED emits the short-wave UV-C light at the correct wavelength of 260 to 280 nanometers. The layer structure is complex, and the interactions between the layers are also complex. How exactly they interact with each other is only known when the chip is ready, but their thickness and composition are determined in advance on a theoretical basis in order to obtain the best possible result.
Finally, everything comes together. The first step is to create a buffer layer, then the active LED layers and finally a contact layer is applied. At this point, relatively fine adjustments can be made to the wavelength of the light. The key is the ratio of aluminum and gallium in the active LED layers.
Troubleshooting with an atomic force microscope
Questions and fresh challenges arise again and again during the fabrication process. Here’s a good example: As soon as the LED structure is built up layer by layer as far as the contact layer it already emits some light, but not enough. The search for a means of adjustment begins. Is the selected structure the best one? Where are the compositions wrong? Where do structures need to be removed or added to make improvements? Where are electrons being lost?
To search for the fault an atomic force microscope may be used to minutely scan the surface of the buffer layers and make the atomic structures visible. Are they smooth or rough? Are there holes or defects caused by particles?
X-rays also show how the layers are composed and where the tensions between them lie. The LED layers are tested for their conductivity. Depending on how well the layers conduct, the developers can tell whether they are on the right track or whether they need to rethink the layers and their composition. Again and again, this means taking one or more steps back or even starting again from scratch and rethinking everything.
Chips no bigger than a grain of sand
This also applies to the next step – chip processing. The wafer produced in the epitaxy process is structured, provided with metal contacts and then divided into small cubes, the chips. The tiny crystals, no bigger than a grain of sand, must be cut out of these wafer. They are the ones that will later emit UV-C light.
As things stand today, however, they do not yet do this efficiently enough. Whereas blue LEDs can achieve an efficiency of well over 60 percent, UV-C-LEDs currently only manage about four percent. For developers, this is still the hardest nut to crack.
Application development:
safely packaging the LED
Alexander Wilm:
is building a house for the LED
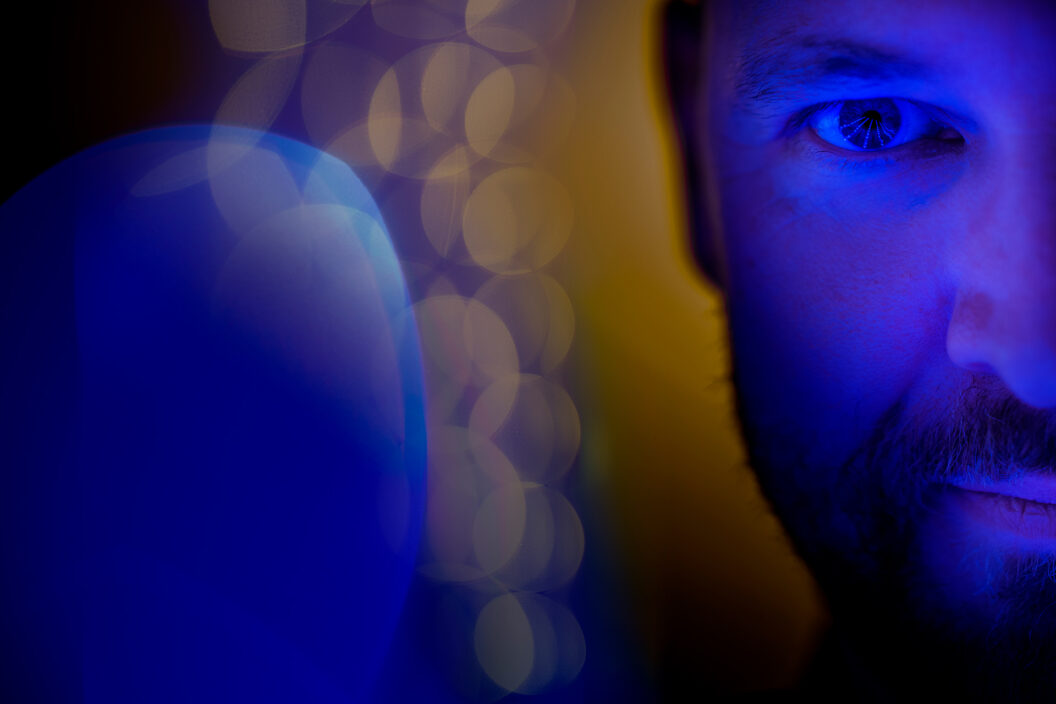
Alexander Wilm needs a challenge. He feels most comfortable in unknown territory: “I like to work on topics that are new to me and help shape future technologies. And as soon as everyone else is doing the same thing, I go looking for something new again,” he says with a smile. Fortunately, there has always been plenty to keep him occupied at Osram in the last 16 years. The LED has accompanied him throughout, or rather he has accompanied the LED – in car headlamps, cell phones, projectors, greenhouses and street lamps. Including a two-year stint in Singapore.
He says he has therefore never had a reason to move to a different employer. Instead, there has always been much to discover and bring to fruition. Like now with the UV-C-LED for disinfection. In Application Engineering, Wilm is the interface between development and the customers. In other words, he discusses concepts and prototypes with a customer and takes the customer’s wishes and requirements back to his colleagues to then work out with them whether they are feasible.
Just spinning around
He likes the mix: “For me, the working environment here is incredibly good and creative. I need an environment in which I can think freely and that’s what I’ve got here. Anyone who wants to develop high-tech solutions needs the space to freely spin things around and around.” That’s precisely what he can do so in special creativity workshops. “The aim is to escape from evolutionary development and create something completely new. Take a completely different approach.”
“We have to escape from evolutionary development and create something completely new. Take a completely different approach.”
You should not be afraid to make mistakes, and you should have the courage to engage in a free and frank dialog: “I’m a fan of talking through problems. If something isn’t working you have to say so without hesitation. At the end of the day, we can learn a lot from that.”
Taming light
The evening is Wilm’s favorite time for tackling tricky problems: “Whenever I need to get to grips with a topic, I usually find a quiet time in the evening away from work,” he says. Sometimes he thinks about the responsibility of developing the UV-C-LED. “The technology is not exactly harmless. The LED needs to be used responsibly. Control mechanisms and sensor systems will help us. Even here there are plenty of possibilities and plenty of work to do,” says Wilm.
He is convinced that the LED will keep him busy in this and other applications for a while. “I believe that we are only just starting to appreciate what the LED as a light source can do, as it is so versatile and universal. There are so many new ideas and concepts to explore. It would be fun for me to journey into more of this uncharted territory.”
Well protected:
the package
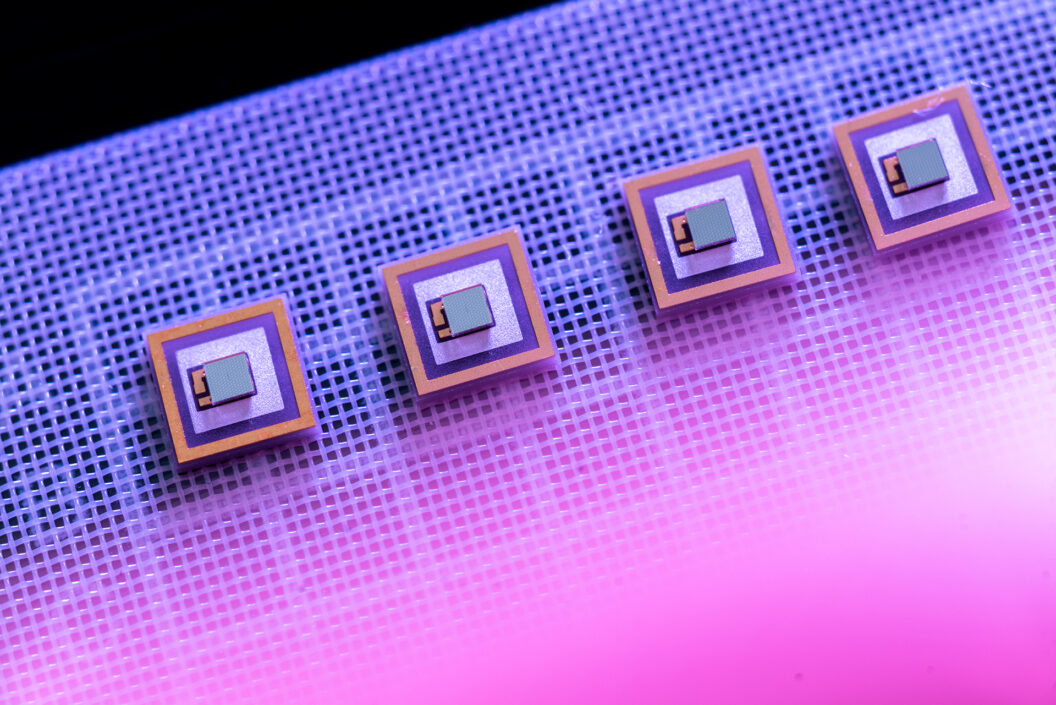
A chip by itself is extremely delicate. It needs protection, and that protection is known as a package. The package has a number of functions. It provides the electrical connection to deliver power to the LED. It also ensures that a placement machine can pick up the LED and place it on a pcb without damaging it. At the same time, it performs optical functions. With a small reflector in the package, it is possible to direct the light or radiation.
Hot stuff
Thermal management plays an important role in the design of the package. Because the hotter an LED gets, the faster it ages. Only four percent of the electrical energy that is fed into the LED is emitted as UV-C radiation, the rest is power loss – and that generates heat. This means that the package has to remove as much heat from the chip as possible. The better it can do this, the cooler the chip stays and the longer it will last. This is a critical point for the development process because a larger package, for example, will lead to better heat dissipation, but larger often means more expensive.
Developers simulate whether and how well thermal management will work before they build prototypes. They begin this process with very broad brushstrokes, exploring different concepts. Finite element methods help them to assess the effects of material interactions. The 3D element to be computed is broken down into smaller elements which are then analyzed for their physical behavior. This is important because the individual materials that make up the package have different coefficients of expansion. This leads to internal tensions as the temperature rises. Simulations can determine whether the connection points will withstand these tensions so that design solutions can be found if necessary. Small features such as angled or rounded edges often influence how well tensions can be mitigated.
Shaping the light
Depending on the application in which the UV-C light is to be later used for disinfection, the emission characteristics also have to be tailored. Among other things, the emitted light can either be fanned out widely or bundled tightly. If, for example, water or air passing over the LED is to be purified, it is advisable not to closely cluster the radiation source but to distribute it along a water or ventilation pipe so that the medium is uniformly irradiated. In contrast, disinfection of water at a faucet or objects in small portable boxes requires significantly smaller and concentrated flows of radiation. This can be achieved through the design of the package.
Rethinking is also the order of the day when it comes to selecting the materials for the package. Simply adopting the materials used for conventional LEDs will not work because the plastics and organic encapsulation materials used for those LEDs would decompose due to the high-energy radiation of the UV-C light. So developers look for materials that will produce a stable, solid and durable package. Ceramics, glass and metalized foils have proved their worth to date.
Test to failure
If a package variant seems promising in the simulation it will be built as a prototype and must survive destructive testing. In this test, the package is subjected to increasing loads until it fails. It is exposed to significantly more sever operating conditions and loads than would occur in the real environment. Endurance tests reveal whether joints are deteriorating and how the material is aging. This in turn allows conclusions to be drawn about the life of the LED.
Once all the requirements have been defined and the package has been designed, the production department will check whether the package can be produced in large quantities. If so, that signals the end of the development project and the start of series production.
Product development:
applications for the LED
André Köhler:
switches on UV-C light
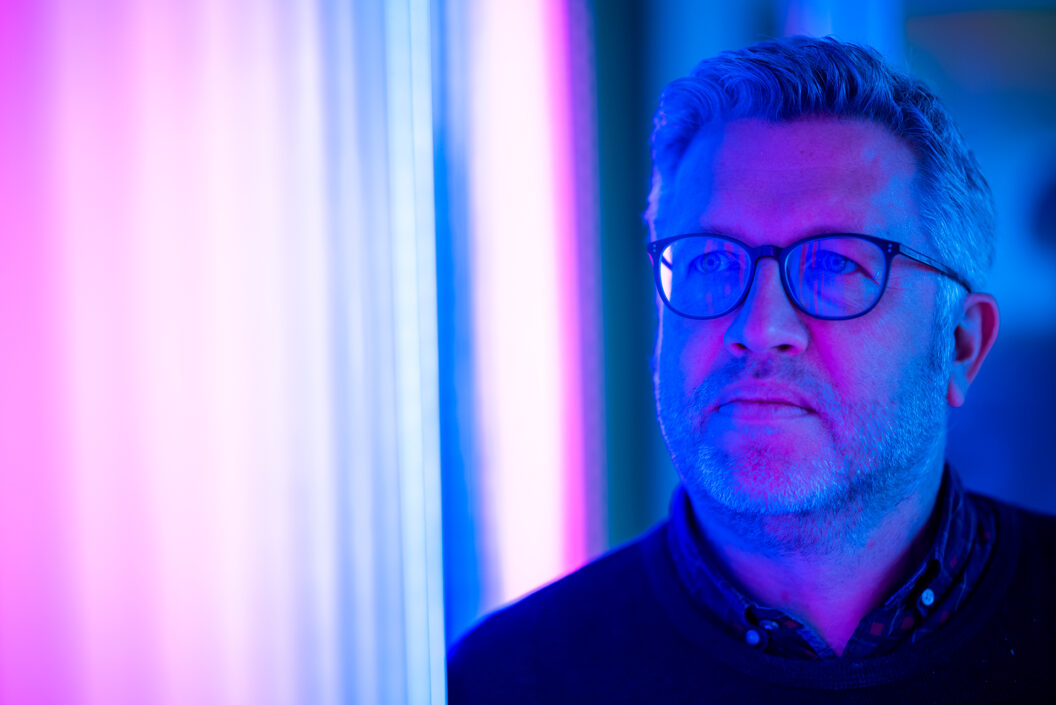
André Köhler wanted to study at the Film and Television College in Babelsberg because he had always been fascination by the cinema and movie production. Instead, he studied economics, sociology and psychology. But he never lost his fascination for what light could do.
When OSRAM relocated its specialty lamp business to Berlin in 2000, Köhler said to himself: “I think I’ll apply there.” A short time later he started in sales, became a product manager and was then closer to his passion for film and television: “Our products opened the doors to movie sets and cinemas. I enjoy the customer environment and the applications. I could never have seen myself in general lighting, but special lamps and contact with end customers are exciting.”
Complete device instead of a component
Special lamps also include those that emit UV-C radiation. They have been at the top of Köhler’s task list for over two years. “The market is crying out for this means of disinfection. Many new companies are now working on the technology, but need help with integrating the lamps. As a result, we suddenly find ourselves in the role of equipment manufacturer and are more involved as consultants,” says Köhler.
“The market is crying out for UV-C as a means of disinfection.”
The time pressure is enormous because unless you’re quick you’ll miss the market.” This is why lots of things run in parallel. That’s particularly true for him as he coordinates everyone involved in development, production and logistics. “I am basically a person who needs calmness and structure, but in stressful situations I adapt,” he adds. “In the past, OSRAM was the supertanker gliding across the sea. Changes came slowly but always after much consideration. Things are different now. Markets are changing rapidly and competition is fierce. Now we need to react quickly to new circumstances. “We can no longer take two years to develop a UV-C device and then launch it on the market. Those days are long gone. We have to adapt the processes and often take a fairly pragmatic approach.”
His team is currently working on a UV-C product portfolio – for a whole new target group. “Up to now, our customers have been professional users, but now we are selling to private customers. That means we need to use entirely different sales channels and sell via online platforms such as Amazon. This is still new territory for us.”
Don’t panic!
There is also a need to rethink the safety features for devices with UV-C light. They have to be designed so that even private users can use them safely. Köhler believes that is both a challenge and a great opportunity: “We no longer only supply the source of radiation, but also offer complete solutions including sensors.”
For Köhler, close coordination with his colleagues is an essential element along the path to a new product. Especially when things get tricky. His approach is to let things sink in for a while, avoid panicking and work out with the team what a solution might look like. “It’s important for me to keep motivating people,“ says Köhler. “I’m basically a positive person – my glass is always half full. Every setback is an experience and can be overcome. As the leader, I try to convey this to my team. The really important ingredient is humor. Humor always helps me to pull myself out of difficult situations.”
In use:
UV-C-products

Products with conventional lamps as sources of UV-C are already available. OSRAM’s AirZing is one of them. First developed for the Chinese market, the device was initially used in early 2020 to disinfect the air in the hospitals set up in Wuhan during the intense phase of the corona pandemic. AirZing is now being used throughout the world. If there are no people in a room, the device is switched on and cleans the air and surfaces with its UV-C radiation. As soon as someone enters the room, sensors detect this movement and immediately turn off the light to prevent damage to skin and eyes.
The issue of efficiency
But these devices are still equipped with conventional discharge lamps that produce UV-C light. The efficiency of the LEDs is not yet good enough to flood large rooms with UV-C light. For a conventional lamp with 30 W of electrical power, efficiency is between 30 and 40 percent, which equates to about twelve watts of UV-C output. If you want to replace a 30 W lamp for disinfecting a room, you would need a large number of LEDs. That would not make economic sense. Replacing a lamp with an LED is just not possible yet.
The LED is ideal, however, for use in mobile applications. It is compact, shatter-proof, vibration-resistant and does not contain mercury. For developers that’s reason enough to create devices in which the LED does a good job even with low efficiency. A compact device for disinfecting small areas is a promising concept.
Small areas at the start
The idea here is for UV-C light to disinfect the air in a room by means of permanent circulation. The used air is drawn into the device where it is sterilized and then directed back into the room. To disinfect a defined volume of space, a certain UV-C output is required and a certain velocity at which the air is channeled past the UV-C source.
With a normal LED unit this is not possible due to the low efficiency and the high cost. The solution: a HEPA filter (high-efficiency air filter) installed upstream of the UV-C LEDs to trap the viruses. This germ trap is then cleaned by a small UV-C LED unit. Instead of disinfecting all the air, the UV-C light shines only on the filter and sterilizes it. LEDs could therefore soon be operating in large areas.
Research is also being carried out on small devices, such as a UV-C LED box in which the light removes viruses and germs from the surfaces of cell phones and other objects. That would be a “germ killer to go”.
OSRAM Licht AG
OSRAM makes the world brighter. With around 21,000 employees worldwide, the Munich-based company is developing applications for the future in its three business units (Opto Semiconductors, Automotive and Digital). What does it need? An eye to the future, visible and invisible light and brilliant employees. Its lamps and LEDs illuminate so many different things including greenhouses, cars, cinemas, runways, streets and even cycling clothes. And they make viruses harmless with UV-C light.