Ein Entwicklerteam von OSRAM erschafft Licht, das es auf der Erde eigentlich gar nicht gibt, um Oberflächen, Raumluft oder Wasser mit UV-C Licht zu entkeimen. Das Rezept: Geballtes Fachwissen, den Mut neu zu denken und die Leuchtdiode.
Für zehn Minuten das Licht anknipsen und schon ist die Raumluft gereinigt? Das Handy in ein Kästchen gelegt und nach wenigen Minuten ist es keimfrei? Was futuristisch anmutet, ist bereits Realität: Die Entkeimung mit kurzwelliger Ultraviolettstrahlung, dem UV-C-Licht.
Dabei gibt es UV-C-Strahlung auf der Erde eigentlich gar nicht. Sie wird von der Ozonschicht absorbiert. Und das ist auch gut so, denn das kurzwellige Licht ist besonders energiereich und sorgt dafür, dass die chemischen Bindungen in der RNA oder DNA-Helix aufbrechen. Eine Weitergabe der Erbinformation wird so verhindert. Mit dem positiven Effekt, dass Viren oder Bakterien nicht mehr infektiös sind und sich nicht vermehren können. Diese Eigenschaft macht UV-C-Licht für die Entkeimung zu einem vielversprechenden Werkzeug.
Doch die Strahlung zersetzt nicht nur nicht nur schädliche Mikroorgansimen, sie kann auch beim Menschen schwerwiegende Schäden an Haut oder Augen verursachen. Ohne Schutzkleidung ist der Kontakt mit UV-C-Licht gefährlich.
In Systemen, die die Raumluft mit der Kraft des Lichts reinigen, stecken momentan noch herkömmliche Gasentladungslampen als Lichtquelle. Die haben allerdings einen entscheidenden Nachteil: Gehen sie zu Bruch, kann Quecksilber austreten. Für mobile Anwendungen sind sie darum nur bedingt geeignet. Anders die Leuchtdiode, kurz: LED. Sie ist klein, flexibel, langlebig und vibrationsresistent – und sie kann UV-C-Licht emittieren. Der Keimkiller für die Jackentasche ist damit in greifbarer Nähe. Die aktuelle Herausforderung: Effizienz. Mit einem Wirkungsgrad von derzeit vier Prozent steckt in der UV-C-LED noch deutliches Verbesserungspotential. Darauf fokussiert das Osram-Team derzeit seine Arbeit.
Die Entwickler*innen von OSRAM arbeiten daran, das zu ändern. Eine Aufgabe, die Kreativität, Ausdauer und Leidensfähigkeit erfordert. Und das Team genau deswegen besonders reizt.
Wer steckt hinter der Technik?
Hightech braucht Menschen. Und diese Menschen brauchen Hightech. Finden Sie selbst heraus, welche kreativen Köpfe hinter der Technik der UV-C-LED stecken und legen Sie den Schalter um.
Vorentwicklung:
Die Suche nach dem perfekten Halbleiter.
Hans-Jürgen Lugauer:
bringt Halbleiter zum Leuchten
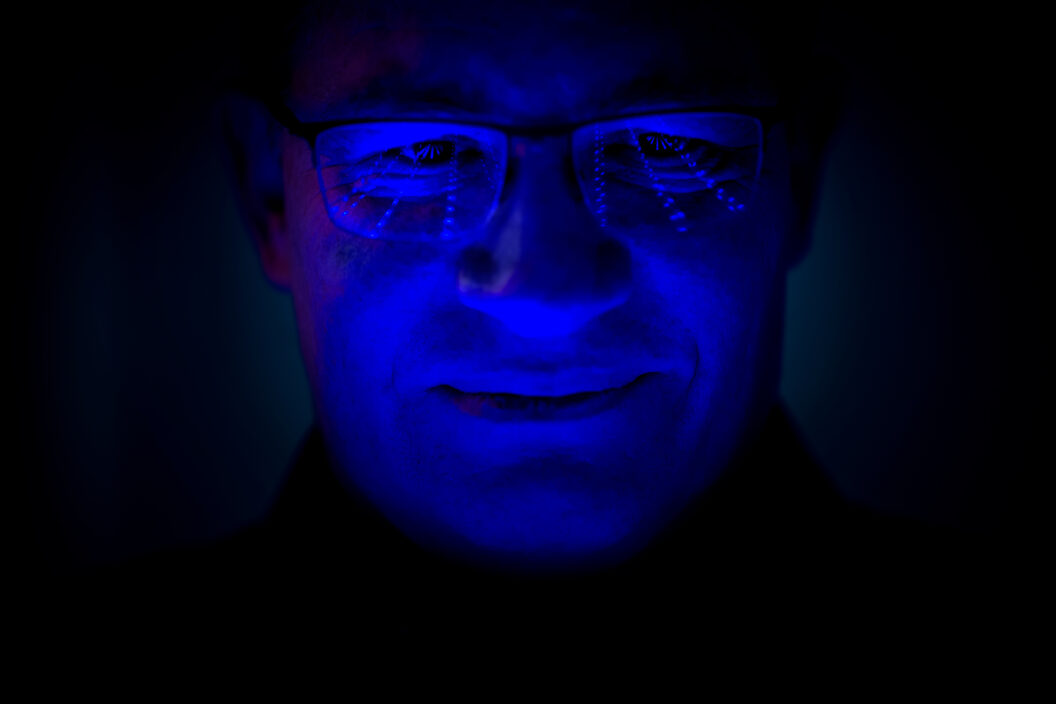
Rückschläge ist Hans-Jürgen Lugauer gewohnt. „Wenn man mit denen nicht umgehen kann, ist man in der Vorentwicklung falsch aufgehoben“, sagt er. Lugauer weiß, wovon er spricht. Schließlich macht er seine Arbeit bei Osram seit 1999. Es war seine erste und einzige Bewerbung nach der Promotion an der Uni Würzburg und für Lugauer bis heute ein ‚perfect match‘.
„Der Job macht mir unglaublich viel Spaß, das passt perfekt für mich. Natürlich gibt es auch mal Phasen, in denen es nicht so super läuft und ich viel Arbeit investiere und dann trotzdem nochmals von vorne anfange, damit muss ich umgehen können.“ Anders könnte er es sich aber auch nicht vorstellen: „Ich möchte nichts machen, von dem ich nicht weiß, warum ich das mache. Auch ein Routinejob wäre nichts für mich – ich brauche schon eine gewisse Challenge.“ Nach seiner Entwicklungsarbeit an LEDs für den sichtbaren Bereich heißt diese Herausforderung nun LEDs zu entwickeln, die UV-C-Licht emittieren.
Spaß am Knacken harter Nüsse
Lugauers Aufgaben haben sich mittlerweile verändert. Er sitzt mehr am Schreibtisch und ist weniger im Labor. Fehlt ihm dieses Selbermachen? „Ja, das vermisse ich tatsächlich. Es juckt mich immer wieder, selbst aktiv etwas zu machen. Ich versuche aber so nah wie möglich an der Technologie zu sein, damit ich Probleme auch noch im Detail verstehen kann. Ein reiner Managementjob ohne technischen Bezug wäre nichts für mich“, betont er.
„Ich versuche so nah wie möglich an der Technologie zu sein, um Probleme im Detail zu verstehen.“
Wird es mal wirklich kniffelig, zieht er sich gerne erst einmal allein zurück, um zu verstehen, an was es hakt – und seinen Ansatz danach im Team zu diskutieren. Ohne die Interaktion mit den Kolleginnen und Kollegen ginge es für ihn nicht. Das sei eine der wichtigsten Komponenten bei seiner Arbeit.
Überhaupt mag er das gemeinsame kreative Arbeiten, das in der Vorentwicklung möglich und nötig ist: „Ich bin kreativ, was auch mit etwas Unstrukturiertheit einhergeht. Ich arbeite hart daran, sie in Grenzen zu halten“, gibt er lachend zu.
Lugauer lacht viel – auch bei der Arbeit: „Mir ist wichtig, dass der Humor nicht zu kurz kommt. Wir lachen oft, auch mal über ganz Alltägliches. Das motiviert mich und meine Kollegen. Wenn ich keinen Spaß hätte, wäre ich nicht zufrieden.“
Licht mit gesellschaftlicher Relevanz
Mit diesem motivierten Team erschafft er nun Licht, das Viren unschädlich macht. Das gibt seiner Arbeit nochmals eine besonderen Sinn, sagt Lugauer: „Es fühlt sich gut an, dass bald kleine, mobile Geräte mit UV-C-Licht in Räumen Luft entkeimen und so, zum Beispiel im Krankenhaus dafür sorgen können, dass weniger Menschen an Bakterien und Viren sterben. Wir entwickeln hier was sozial und gesellschaftlich wirklich Relevantes. Mit UV-C-LEDs können wir es schaffen, die bisher verwendeten Quecksilberlampen abzulösen. Das wäre ein Riesensprung nach vorne für die Gesundheit der Bevölkerung und die Umwelt. Das gibt mir ein extrem gutes Gefühl.“
Die Basis:
der Halbleiterkristall

Aluminiumgalliumnitrid, kurz: AlGaN, ist die Basis für das UV-C-Licht. Dieses Halbleiterkristall ist eine Verbindung aus Aluminium, Gallium und Stickstoff. Damit unterscheiden sich UV-C-LED bereits grundsätzlich von blauen LED, auf denen die handelsüblichen weißen LED aufbauen. Letztere basieren auf Indiumgalliumnitrid (InGaN). Für das UV-C-Licht tauschten die Entwickler also das Indium gegen das Aluminium. So einfach? Nein, denn die Materialeigenschaften der beiden Verbindungen unterscheiden sich. AlGaN verhält sich daher auch völlig anders als InGaN. Es braucht also auch neue Entwicklungs- und Herstellungsprozesse.
Der Isolator soll leuchten
Die große Herausforderung: das Material zum Leuchten zu bringen. Per se tut es das nicht – der Hableiter AlGaN ist auch bei Raumtemperatur noch ein sehr guter Isolator. Erst durch das gezielte Zumischen von Atomen wird aus dem quasi nichtleitenden ein leitendes Material. Dieser Herstellungsprozess nennt sich Epitaxie. Bei dem chemischen Abscheidungsverfahren werden die Ausgangsmaterialien gasförmig in einen Reaktor geleitet. Dort reagieren sie unter extrem hohen Temperaturen von weit über 1.100 Grad Celsius auf einer passenden Unterlage, dem sogenannten Substrat, miteinander.
Das in der Halbleiterwelt übliche Silizium ist dabei als Substrat ungeeignet, da sich die Gitterabstände der beiden Kristalle zu sehr unterscheiden und es UV-C Strahlung absorbiert. Für blaue, grüne und weiße LEDs auf InGaN-Basis kommt daher meist Aluminiumoxid Al2O3, auch Saphir genannt, zum Einsatz. Auch für Aluminiumgalliumnitrid ist Saphir für die Erzeugung von UV-C-Licht das Substrat der Wahl. Denn seine physikalischen Eigenschaften passen sehr gut zu denen des Halbleiters. Außerdem ist es transparent für die UV-C Strahlung.
Hauchdünn geschichtet
Der Epitaxieprozess selbst gleicht weitgehend dem bei der Herstellung einer konventionellen LED: Es werden weit über hundert hauchdünne Schichten aufeinander abgeschieden. Die wichtigsten, die sogenannten „Quantentröge“, sind dabei dünner als zehn Atomlagen. Damit die LED am Ende das kurzwellige UV-C-Licht in der richtigen Wellenlänge von 260-280 Nanometer emittiert, ist aber viel theoretische Vorarbeit gefragt. Die Schichtstruktur ist komplex, die Wechselwirkungen zwischen den Schichten sind es ebenfalls. Wie genau sie miteinander interagieren weiß man erst, wenn der Chip fertig ist, doch ihre Dicke und Zusammensetzung werden vorab auf theoretischer Basis betrachtet, um das bestmögliche Ergebnis zu erhalten.
Schließlich ist es soweit: Als erstes entsteht eine Pufferschicht, dann folgen die aktiven LED-Schichten und am Ende wird eine Kontaktschicht aufgetragen. An diesem Punkt lässt sich die Wellenlänge des Lichts bereits relativ fein einstellen. Die Stellschraube: das Mischverhältnis von Aluminium und Gallium in den aktiven LED-Schichten.
Fehlersuche unter dem Rasterkraftmikroskop
Immer wieder tauchen während des Herstellungsprozesses Fragen und neue Herausforderungen auf. Ein Beispiel: Sobald die LED-Struktur Schicht für Schicht bis zur Kontaktschicht aufgebaut ist, emittiert sie bereits etwas Licht, aber nicht genug. Die Suche nach wichtigen Stellschrauben beginnt. Ist die gewählte Struktur optimal? Wo passen Zusammensetzungen nicht? Wo müssen Strukturen entfernt oder ergänzt werden, damit es besser wird? Wo gehen die Elektronen verloren?
Auf der Suche nach dem Fehler tastet zum Beispiel ein sogenanntes Atomic Force Microscope die Oberfläche der Pufferschichten fein ab und macht die atomaren Strukturen sichtbar. Ist sie glatt oder ist sie rau? Gibt es Löcher oder Defekte durch Partikel?
Röntgenstrahlen machen außerdem sichtbar, wie die Schichten zusammengesetzt und wie sie gegeneinander verspannt sind. Die LED-Schichten werden auf ihre Leitfähigkeit geprüft. Je nachdem, wie gut die Schichten leiten, wissen die Entwickler, ob sie auf dem richtigen Weg sind, oder ob sie die Schichten und ihre Zusammensetzung neu überdenken müssen. Immer wieder bedeutet das: einen oder mehrere Schritte zurück oder eben auch ganz von vorne anfangen und nochmal alles neu denken.
Chipswürfel in Sandkorngröße
Das gilt auch für den nächsten Schritt, die Chipprozessierung. Die in der Epitaxie gefertigte Scheibe wird dabei strukturiert, mit Metallkontakten versehen und am Ende in kleine Würfelchen, die Chips, vereinzelt. Die winzigen, sandkorngroßen Kristalle müssen aus ihr herausgesägt werden. Sie sind es, die später das UV-C-Licht emittieren.
Stand heute tun sie dies allerdings noch nicht effizient genug. Während blaue LEDs einen Wirkungsrad von weit über 60 Prozent erreichen können, schaffen UV-C-LED aktuell gerade einmal etwa vier Prozent. Für die Entwickler ist das derzeit noch die härteste Nuss, die es zu knacken gilt.
Applikationsentwicklung:
Die LED sicher verpacken
Alexander Wilm:
baut der LED ein Haus
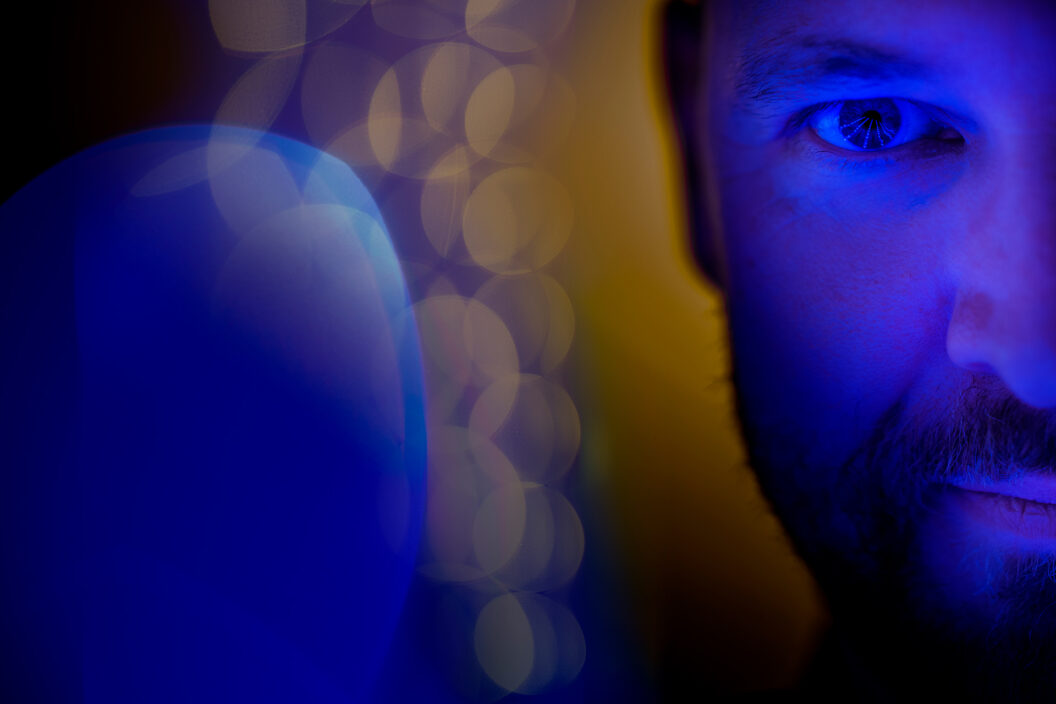
Alexander Wilm braucht die Herausforderung. Am wohlsten fühlt er sich auf unbekanntem Terrain: „Ich arbeite mich gerne in für mich unbekannte Themen ein und gestalte Zukunftstechnologien mit. Wenn es dann alle machen, suche ich mir was Neues“, sagt er und lacht. Glücklicherweise gab es für ihn bei Osram in den letzten 16 Jahren davon immer genug. Die LED hat ihn begleitet oder vielmehr er die LED: In Automobilscheinwerfern, Handys, Beamern, Gewächshäusern und in Straßenlampen. Für zwei Jahre auch in Singapur.
Anlass für einen Wechsel zu einem anderen Arbeitgeber sah er darum nie, sagt er, stattdessen gab es immer viel zu entdecken und voranzubringen. So wie jetzt bei der UV-C-LED für die Entkeimung. Im Application Engineering ist Wilm Schnittstelle zwischen der Entwicklung und den Kunden. Das heißt, er diskutiert Konzepte und Prototypen mit einem Kunden und bringt Wünsche und Anforderungen mit, um sie mit seinen Kollegen auf ihre Machbarkeit abzuklopfen.
Einfach mal rumspinnen
Die Mischung gefällt ihm: „Für mich gibt es hier einfach ein unglaublich gutes und kreatives Arbeitsklima. Ich muss frei denken können und das geht hier. Gerade, wer Hightech entwickeln will, braucht den Raum, um auch mal völlig frei rum zu spinnen.“ In speziellen Kreativitätsworkshops kann er das tun. „Ziel ist es, aus dem evolutionären Weiterentwickeln rauszukommen, und etwas komplett Neues zu schaffen. Mal völlig andere Ansätze zu verfolgen“, erklärt er.
„Wir müssen aus dem evolutionären Weiterentwickeln rauskommen und etwas komplett Neues schaffen. Mal völlig andere Ansätze verfolgen.“
Angst vor Fehlern dürfe man dabei keine haben, stattdessen den Mut zu offener Kommunikation: „Ich bin ein Freund davon, Probleme anzusprechen. Wenn etwas nicht funktioniert, dann muss man das ohne Bedenken auch sagen dürfen. Schließlich können wir daraus viel lernen.“
Licht bändigen
An besonders kniffeligen Problemen knobelt Wilm am liebsten abends: „Wenn ich mich in ein Thema reinfuchsen muss, setze ich mich meistens nochmals hin, wenn ich meine Ruhe habe“, sagt er. Manchmal denkt er da auch über die Verantwortung nach, die die Entwicklung von der UV-C-LED mit sich bringt. „Die Technologie ist nicht ganz ungefährlich. Man muss die LED verantwortungsvoll einsetzen. Kontrollmechanismen und Sensoriksysteme helfen uns dabei. Auch hier reißen die Möglichkeiten und Aufgaben also nicht ab“, sagt Wilm.
Er ist sich sicher, dass ihn die LED auch in anderen Anwendungsbereichen noch eine Weile beschäftigen wird. „Ich glaube mit der LED als Lichtquelle, die so flexibel und universell einsetzbar ist, sind wir gerade erst am Anfang. Es gibt noch so viele neue Ideen und Konzepte. Noch ein paar von diesen neuen Bereichen mit zu begleiten, das würde mir Spaß machen.“
Gut geschützt:
das Package
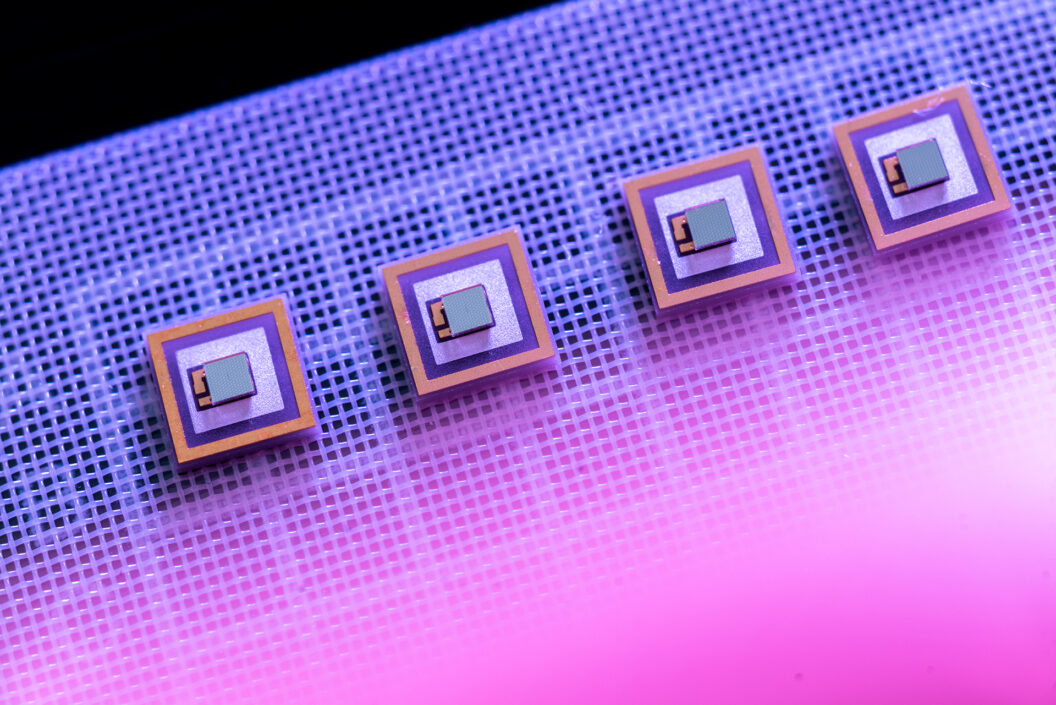
Ist ein Chip vereinzelt, ist er vor allem eines: sehr empfindlich. Zum Schutz bekommt er darum zuerst einmal ein Häuschen, das Package. Das hat unterschiedlichste Aufgaben: Zum einen ermöglicht es den elektrischen Anschluss, um Strom in die LED zu bringen. Es stellt außerdem sicher, dass ein Bestückautomat die LED aufnehmen und auf einer Platine platzieren kann, ohne sie zu beschädigen. Gleichzeitig übernimmt es optische Funktionen. Mit einem kleinen Reflektor im Package kann man bereits Licht- oder Strahlungsrichtungen durchführen.
Heiße Angelegenheit
Bei der Auslegung des Packages spielt das thermische Management eine wichtige Rolle. Denn je heißer eine LED betrieben wird, desto schneller altert sie. Lediglich vier Prozent der elektrischen Energie, die in die LED geleitet wird, emittiert sie als UV-C-Strahlung, der Rest ist Verlustleistung – und die erzeugt Wärme. Für das Package heißt das: es soll die entstehende Wärme so gut wie möglich aus dem Chip ableiten. Je besser das funktioniert, desto kühler bleibt der Chip und desto länger lebt er. Für die Entwicklung ist das ein kritischer Punkt, denn einerseits ermöglicht zum Beispiel ein größeres Package einen optimaleren Wärmefluss, andererseits bedeutet größer oft auch teurer.
Ob und wie gut das thermische Management funktioniert, simulieren die Entwickler bevor sie erste Prototypen bauen. Sie starten zunächst sehr breit, mit unterschiedlichen Konzepten. Finite-Elemente Methoden helfen ihnen dabei, die Materialwechselwirkungen einzuschätzen. Dabei wird der Körper, der berechnet werden soll in kleine Teilkörper zerlegt und diese dann auf ihr physikalisches Verhalten analysiert. Das ist wichtig, denn die Ausdehnungskoeffizienten der einzelnen Materialien, aus denen das Package besteht, unterscheiden sich. Bei Erwärmung führt das zu internen Spannungen. Ob die Verbindungsstellen diesen Stand halten, lässt sich im Vorfeld bereits simulieren und über das Design lösen: Kleine Features wie eckige oder runde Kanten, haben oftmals einen Einfluss darauf, wie gut sich Spannungsspitzen abfedern lassen.
Das Licht formen
Je nachdem, in welcher Anwendung das UV-C-Licht später zur Entkeimung eingesetzt werden soll, muss auch die Abstrahlcharakteristik entsprechend angepasst werden. Das emittierte Licht lässt sich unter anderem sehr breit auffächern oder eng bündeln. Sollen beispielsweise Wasser oder Luft, die an der LED vorbeiströmen gereinigt werden, ist es sinnvoll, die Strahlquelle nicht eng zu clustern, sondern sie entlang eines Wasser- oder Lüftungsrohrs zu verteilen, um das Medium gleichmäßig damit zu bestrahlen. Im Gegensatz dazu erfordert die Entkeimung von Wasser an einem Wasserhahn oder von Gegenständen in kleinen portablen Boxen deutlich kleinere und konzentrierte Strahlungsflüsse. Das lässt sich über das Package realisieren.
Neu denken, heißt es auch bei der Auswahl der Materialien für das Package. Einfach die der konventionellen LEDs zu übernehmen, funktioniert nicht. Denn dort eingesetzte Kunststoffe und organische Vergussmaterialien würde das UV-C-Licht mit seiner hochenergetischen Strahlung zersetzen. Die Entwickler suchen also nach Materialien, die ein stabiles, solides und langlebiges Package ermöglichen. Keramiken, Glas und Metallisierungen haben sich bisher bewährt.
Auf Biegen und Brechen
Überzeugt eine Package-Variante in der Simulation, wird sie als Prototyp aufgebaut und muss erst einmal den sogenannten „Test-to-Failure“ überstehen. Bei diesem Test wird das Package so stark belastet, bis es kaputt geht. Dabei ist es deutlich überhöhten Betriebsbedingungen und Belastungen ausgesetzt – die im realen Umfeld so nicht auftreten würden. In den Härtetests zeigt sich, ob Verbindungsstellen aufgehen und wie das Material altert. Das wiederum lässt Rückschlüsse auf die Lebensdauer der LED zu.
Sind alle Anforderungen definiert und das Package designt, prüft die Fertigung, ob es sich auch in großen Stückzahlen fertigen lässt. Ist das möglich, ist auch das Entwicklungsprojekt abgeschlossen und die Serienfertigung kann beginnen.
Produktentwicklung:
Einsatz für die LED
André Köhler:
knipst das UV-C-Licht an
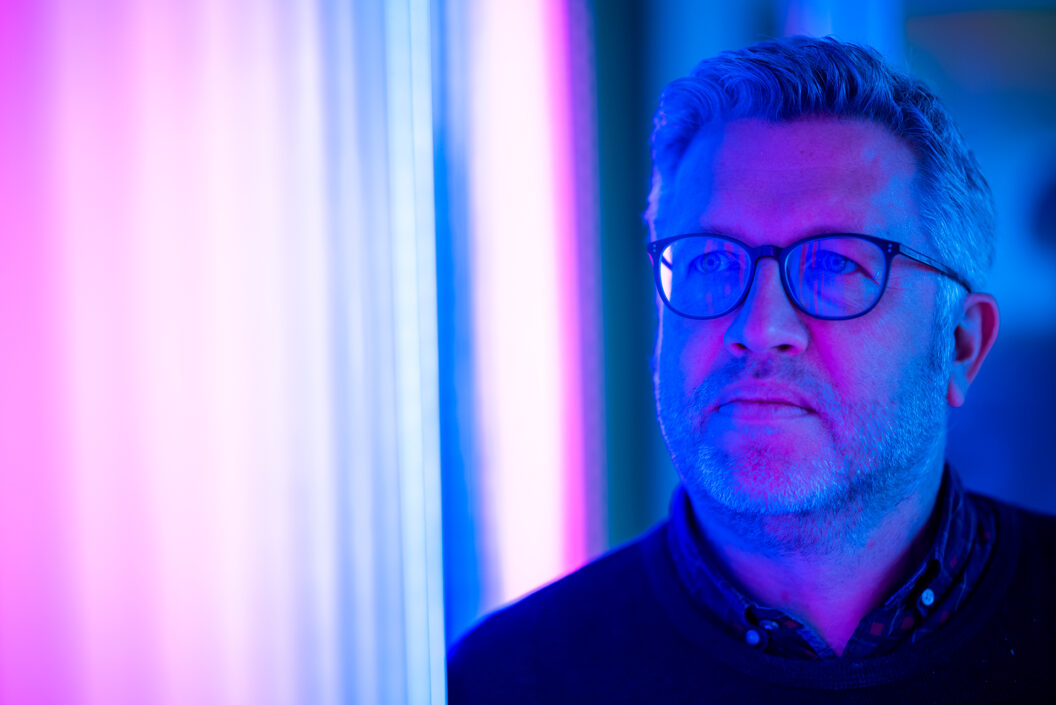
Eigentlich wollte André Köhler ja an der Hochschule für Film und Fernsehen in Babelsberg studieren. Denn das Kino und Filmproduktionen faszinierten ihn. Stattdessen studierte er BWL, Soziologie und Psychologie. Aber die Faszination für das Lichtspiel blieb.
Als OSRAM den Geschäftsbereich für Speziallampen im Jahr 2000 nach Berlin verlegte, stand für Köhler fest: „Da bewerbe ich mich.“ Kurze Zeit später startete er im Vertrieb, wurde Produktmanager – und war damit seiner Leidenschaft für Film und Fernsehen wieder näher: „Unsere Produkte öffneten mir die Türen zu Filmsets und Kinos. Das Kundenumfeld und die Applikationen machen mir Spaß. Ich hätte mich nie im Bereich Allgemeinbeleuchtung gesehen, aber die Speziallampen und der Kontakt zu den Endkunden ist spannend.“
Komplettgerät statt Komponente
Zu den Speziallampen gehören auch die mit UV-C-Strahlung. Sie stehen seit gut zwei Jahren ganz oben auf Köhlers Aufgabenliste. „Der Markt schreit momentan nach dieser Lösung zur Entkeimung. Viele neue Firmen beschäftigen sich jetzt mit der Technologie, benötigen aber Hilfe bei der Integration der Lampen. Dadurch sind wir plötzlich in der Rolle eines Geräteherstellers und stärker beratend tätig“, berichtet Köhler.
„Der Markt schreit momentan nach UV-C als Lösung zur Entkeimung.“
Der Zeitdruck sei groß, denn nur wer schnell ist, mischt auf dem Markt mit.“ Vieles laufe darum parallel. Gerade auch für ihn, der alle Beteiligten aus Entwicklung, Fertigung und Logistik koordiniert. „Ich bin grundsätzlich ein Mensch, der eher Ruhe und Struktur braucht, aber in Stresssituationen passe ich mich an“, betont Köhler. „Früher war OSRAM immer ein großer Tanker, der ruhig durch die See fuhr. Änderungen wurden langsam, aber sehr bewusst vollzogen. Das ist jetzt anders. Die Märkte verändern sich schnell und die Konkurrenz ist groß. Nun heißt es: schnell auf die neuen Gegebenheiten reagieren. „Wir können an einem UV-C-Gerät nicht mehr zwei Jahre entwickeln und es dann in den Markt geben. Die Zeiten sind vorbei. Wir müssen die Prozesse anpassen und oft relativ pragmatisch vorgehen.“
Sein Team arbeitet momentan an einem UV-C-Produktportfolio – für eine ganz neue Zielgruppe. „Bisher waren unsere Kunden professionelle Anwender, jetzt verkaufen wir an Privatkunden. Das heißt, wir müssen ganz andere Vertriebswege nutzen und über Online-Plattformen wie Amazon verkaufen. Das ist für uns noch Neuland.“
Keine Panik!
Neu denken heißt es auch bei den Sicherheitsfeatures für die Geräte mit UV-C-Licht. Diese müssen so ausgelegt sein, dass selbst private Anwender sie gefahrlos einsetzen können. Eine ziemliche Herausforderung und gleichzeitig eine große Chance, findet Köhler: „Wir liefern nicht mehr nur die Strahlquelle sondern bieten Komplettlösungen mit Sensorik an.“
Auf dem Weg zu neuen Produkten ist die enge Abstimmung mit seinen Kolleg*innen für Köhler essenziell. Gerade wenn es einmal kniffelig wird. Seine Devise: Erst einmal sacken lassen, keine Panik und mit dem Team ausloten, wie eine Lösung aussehen könnte. „Für mich ist wichtig, dass ich die Leute immer wieder motiviere“, sagt Köhler. „Ich habe generell eine positive Grundstimmung – für mich ist das Glas halbvoll. Jeder Rückschlag ist eine Erfahrung und kann gemeistert werden. Das versuche ich dem Team als Leiter mitzugeben. Und ganz wichtig dabei: Humor! Humor hilft mir immer, mich auch aus schwierigen Situationen selbst wieder herauszuziehen.“
Im Einsatz:
die UV-C-Produkte

Produkte mit konventionellen Lampen als UV-C-Strahlquelle gibt es bereits. OSRAM‘s AirZing ist eines davon. Zuerst für den chinesischen Markt entwickelt, entkeimte das Gerät am Anfang in Wuhan während der Hochphase der Corona-Pandemie Anfang 2020 die Luft in den dort eingerichteten Krankenhäusern. Inzwischen werden die Geräte weltweit eingesetzt. Ist ein Zimmer menschenleer, wird das Gerät angeschaltet und reinigt mit seiner UV-C-Strahlung die Luft und Oberflächen. Kommt jemand in den Raum, erkennen Sensoren die Bewegung und schalten das Licht sofort ab, um Schäden an Haut und Augen zu vermeiden.
Die Sache mit der Effizienz
Doch bisher stecken in diesen Geräten noch konventionelle Entladungslampen, die UV-C-Licht erzeugen. Denn die Effizienz der LED reicht bisher nicht, um größere Räume mit UV-C-Licht zu bestrahlen. Bei einer konventionellen Lampe mit 30 Watt elektrischer Leistung liegt die Effizienz zwischen 30 und 40 Prozent, das sind etwa zwölf Watt UV-C Leistung. Will man zum Beispiel eine 30 Watt Lampe ersetzen, mit der ein Raum entkeimt wird, bräuchte es aktuell noch sehr viele LEDs. Das ist ökonomisch nicht sinnvoll. Lampe raus, LED rein – das geht noch nicht.
Dabei ist die LED gerade für den Einsatz in mobilen Anwendungen perfekt geeignet. Sie ist kompakt, bruchsicher, vibrationsresistent und kommt ohne Quecksilber aus. Für die Entwickler Grund genug, an Geräten zu feilen, in denen die LED auch mit geringerer Effizienz einen guten Job macht. Ein vielversprechendes Konzept: ein kompaktes Gerät zur Entkeimung von kleineren Flächen.
Kleine Flächen für den Anfang
Die Idee dahinter: Die UV-C-Lichtlösung zur Entkeimung der Raumluft arbeitet mit einer permanenten Zirkulation. Die verbrauchte Luft wird eingesaugt, im Gerät entkeimt und dann wieder in den Raum geleitet. Um ein definiertes Raumvolumen zu desinfizieren ist eine gewisse UV-C-Leistung erforderlich und eine bestimmte Luftgeschwindigkeit, mit der die Luft an der UV-C-Luftquelle vorbeigeleitet wird.
Mit einer normalen LED-Einheit ist das aufgrund der geringen Effizienz und der hohen Kosten nicht möglich. Die Lösung: Vor den UV-C-LEDs wird ein High-Efficiency Particulate Air-Filter, kurz: HEPA-Filter, eingebaut, der die Viren aufnimmt. Diesen zusätzlichen Keimblocker reinigt dann eine kleine UV-C-LED-Einheit. Statt die komplette Luft zu entkeimen, strahlt das UV-C-Licht also nur auf den Filter und entkeimt diesen. So könnten LEDs schon bald Aufgaben in größeren Anlagen übernehmen.
Geforscht wird außerdem an kleinen Geräten, wie einer UV-C-LED-Box in der das Licht die Oberflächen von Handys oder anderen Gegenständen von Viren und Keimen befreit. Das wäre dann der „Keimkiller To-go“.
OSRAM Licht AG
OSRAM macht die Welt heller. Mit weltweit rund 21.000 Mitarbeiter*innen entwickelt das Münchner Unternehmen in drei Geschäftsbereichen (Opto Semiconductors, Automotive und Digital) Anwendungen für die Zukunft. Was es dafür braucht? Den Blick nach vorne, Sichtbares und unsichtbares Licht und brillante Mitarbeiter. Die Lampen und LEDs beleuchten unter anderem Gewächshäuser, Autos, Kinos, Landebahnen, Straßen oder auch Radkleidung. Und sie machen Viren mit UV-C-Licht unschädlich.